Prescriptive Approach
Steve Welch talks to Mark Costello about Synecco’s design processes and work in the medical device sector for New Design Magazine.
Mark Costello is Head of Design at Synecco, responsible for creating better product experiences for their customers and users through industrial design, usability design and product engineering.
Synecco was founded in Ireland in 2004 initially providing managed manufacturing services in China for US and European customers across a range of sectors. In 2007 focus shifted to the medical device industry and in 2009 Synecco opened its design offices at the Galway headquarters. This enabled them to provide turnkey design, development and manufacturing solutions. In 2017 Synecco acquired a manufacturing facility in Ireland allowing for the more localized design to manufacturing solutions.
Steve Welch: What are your company’s key activities within the medical / healthcare sector? Is this your main focus?
Mark Costello: Life Sciences (Medical, Pharmaceutical, Diagnostics) has become the focus of Synecco and represents more than 75% of what we do. Outside of this our Irish manufacturing site still maintains an automotive capability and our industrial design team’s remit can at times extend into consumer and industrial products for legacy customers. In the design and development group, we work on quite a lot of hand-held devices used to carry out medical procedures, we’re also working on wearable and IOMT devices where usability and aesthetics are critical.
SW: How does designing for medical devices differ to your work in other sectors (such as consumer or industrial)?
MC: The key difference is risk management, which leads to increased regulations, testing, trials and documentation for our customers, their suppliers and every process and subprocess within the system. These regulations extend to design and usability. Regulatory bodies require a UEF (Usability Engineering File) to be submitted as part of the regulatory approvals process in compliance with IEC 62366 and the FDA guidance document: “Applying Human Factors and Usability Engineering to Medical Devices”. This is a much more formal approach to usability than what we see in consumer or most industrial sectors. For the higher risk devices this culminates in a large cohort of users engaging in unprompted simulated use studies. At the core of this is the shift from labelling the issues as a user error to a use error, with the latter placing the responsibility for mitigation of use risk with the manufacturer.
This rigor on usability wasn’t always the case in the medical device industry. IEC 62366 was introduced to address the usability deficit in the medical device industry. This wasn’t published until 2007, so the industry has been playing catch up. For example, when I worked at LG Electronics from 1999-2002, we’d run observational usability sessions with a cross section of European consumers on products as basic as microwave ovens. This however was driven not by risk but by the need to differentiate in a fast-moving competitive market. Another key difference is that more so than in other sectors the role of the designer can be easily underestimated in the medical device industry due to the understandable focus on quality, science and technology. We make the case that the function of design is to control the reaction of people, whether it’s how the device looks or how it’s used during pressurized situations. We see the function of engineering as one that controls technology, i.e. the medical procedure, the device function and reliability or the process by which it is manufactured.
SW: What are the commonalities with other design sectors?
MC: Aside from risk, regulatory and quality focus, and associated documentation the key building blocks of a good design process is essentially common across medical, industrial and consumer sectors. Observation-based research to gain user insights, defining user needs, idea generation to solve those needs, iterative prototyping, user testing and functional testing are still critical in the development of successful medical products.
SW: What do you see as the key trends in the medical sector?
MC: From a design point of view, it’s encouraging to see an increase in the awareness of putting human factors at the core of every device, this shift has been helped in part by the standards, but also by increased competition driving differentiation which brings with it an increased awareness of the importance of how devices are perceived.
We are also seeing a trend towards personalised healthcare in the home environment, whether these are early diagnosis via sophisticated monitoring or the management of medication compliance. The goal being to keep people healthier for longer and away from overloaded acute hospital care. As populations age in the developed world, this approach will be essential in preventing our health services from being overwhelmed.
This personal and home-based healthcare has the effect of blurring the lines between consumer and medical products. As the expectations and sophistication of healthcare consumers increases so too does the user centred demands on the traditional medical device manufacturers. This has also opened a door to new competition from outside of the industry. This is currently most evident in the IOMT (Internet of Medical Things) space e.g. Apple but it’s influencing all types of medical products.
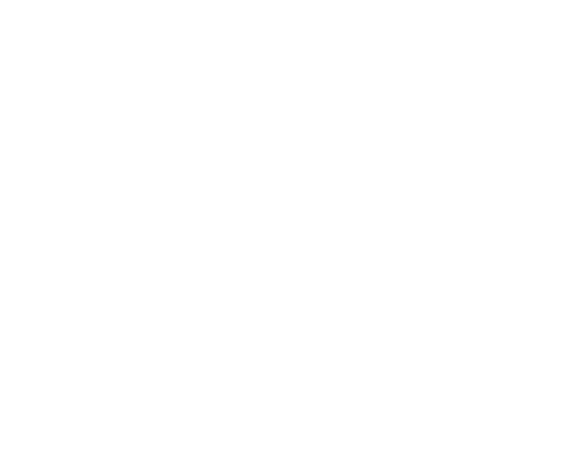
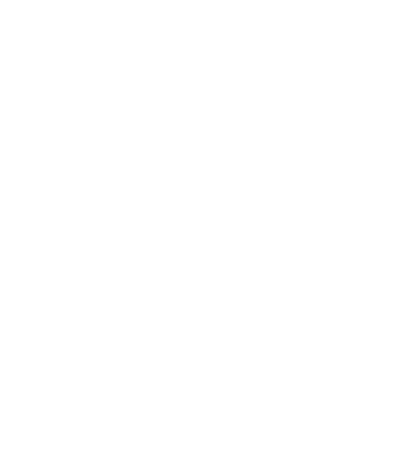
SW: Who in the main are your clients – are there more stakeholders involved in the design process?
MC: We have a range of customers of all shapes and sizes from the well-known companies like Medtronic to SMEs, to Start-ups. This mix certainly makes things interesting and keeps us sharp but can also be a challenge in that our customers’ needs, and their internal capabilities can vary hugely meaning that our services need to be adaptable.
Medical devices programs tend to have similar stakeholders to non-medical, but the emphasis and level of stakeholder engagement differs in that Quality, Regulatory and risk management matters
are always to the fore. We typically work with, clinicians, patients, regulatory teams, marketing teams, engineering / R&D teams and inventor CEOs. When dealing with organisations that don’t have a design function, we often find our design team as the catalyst for better communication between key stakeholders that struggle to find a common language e.g. in-house engineering and marketing teams.
SW: What is your strategy for research, development and the innovation process within the medical sector?
MC: At the core of our process is a typical design thinking approach which puts the human aspect of the program front and centre and allows us to learn, fail and succeed fast. We start with empathising with the user (patient or clinician), defining their needs, generating ideas to meet their needs and the other project constraints, prototyping, starting with low resolution high iteration prototypes. We then return to the user with the prototypes – allowing us to empathise further and repeat the cycle. Our design SOP aligns this process to IEC 62366 standard to ensure that the UEF is auditable and fit for submission.
SW: How is digital design/ 3D printing / the internet of things being incorporated into the design of medical devices?
MC: 3d CAD, visualisation and simulation packages are essential design tools that are advancing all the time and will be further enhanced with the use of virtual and augmented reality. However, regardless of how good these virtual environments get 3D printing is still key as designers, engineers and users of physical devices, need to get these ideas off the screen and into the hand as rapidly as possible. 3d printing is now no different for our design teams than 2d printing was a decade or so ago, we 3d print in house daily to explore new ideas in 3d to facilitate rapid learning.
As regards IOMT, this is introducing a raft of new smart devices and transforming existing devices such as inhalers, thermometers, blood pressure cuffs into smart devices. These new devices need graphical touch-based user interfaces, the challenge for designers is to create interfaces that are engaging yet have been designed with the rigorous risk averse approach required for a medical device.
SW: Could you provide some more detail about a case study and what were the challenges and the issues it set out to solve ?
MC: Project and product lifecycles in the medical device industry are long due to the regulatory process. As a result, we find ourselves working on very interesting programs in 2019 that we won’t be able to talk about until 2023. This creates a real issue for our marketing team. We therefore developed the Hummingbird device internally to represent the type of projects we’re working on but without breaching confidentiality.
The Hummingbird story is a typical one for us. Our customer is developing a device that carries out a procedure and needs to optimise how the clinician interacts with the device. In this case the therapy we chose was the delivery of a stent (80% of the worlds arterial and venous stents are manufactured in Ireland). We observed clinicians at work and identified that they wanted fine control at initial release and more macro control for the remainder of the procedure. The thumbwheel is a widely accepted means of releasing a stent by pulling back the sheath encasing it, however it is not the ideal mechanism for the sustained action and forces that we see with longer stents. We therefore coupled the thumbwheel with a lever, activated when needed enabling the user to use the larger muscles of the forearm to do the heavy work. A switching mechanism between both functions ensured inherent safety by design.
This usability led mechanical system is housed in an unintimidating dynamic form with muted colours. It is split top and bottom defining its dual function zones. The bottom half is a soft touch material designed to sit comfortable in the user’s palm. Industrial Design intertwines with the usability and mechanical design so that the 3 are inextricably linked.
We often remind our customers that Industrial Design is not a veneer of nice forms but rather it’s about using aesthetics strategically. Decide what you want a device to say (i.e. use this way, I’m a reliable instrument, I’m an approachable device, my technology is cutting edge etc.), then use the language of form, colour and texture to convey this message.